Robots are capable of examining the facilities in greater detail than humans, engineers say. ‘Finding defects is like finding a needle at sea. Some are in hidden places or dead corners, and they can easily be missed by humans,’ Wong says. — SCMP
Hong Kong electricity provider CLP Power has said its five-drone fleet and crawler robot have reduced facility inspection times at its power plants, adding that the technology has also helped cut expenses.
Company engineers said the equipment had cut inspection times from 12 to one or two days in some instances and resulted in more flexible arrangements for carrying out checks.
Robots were capable of examining the facilities in greater detail than humans and could help reduce safety hazards for workers operating in confined areas, they added.
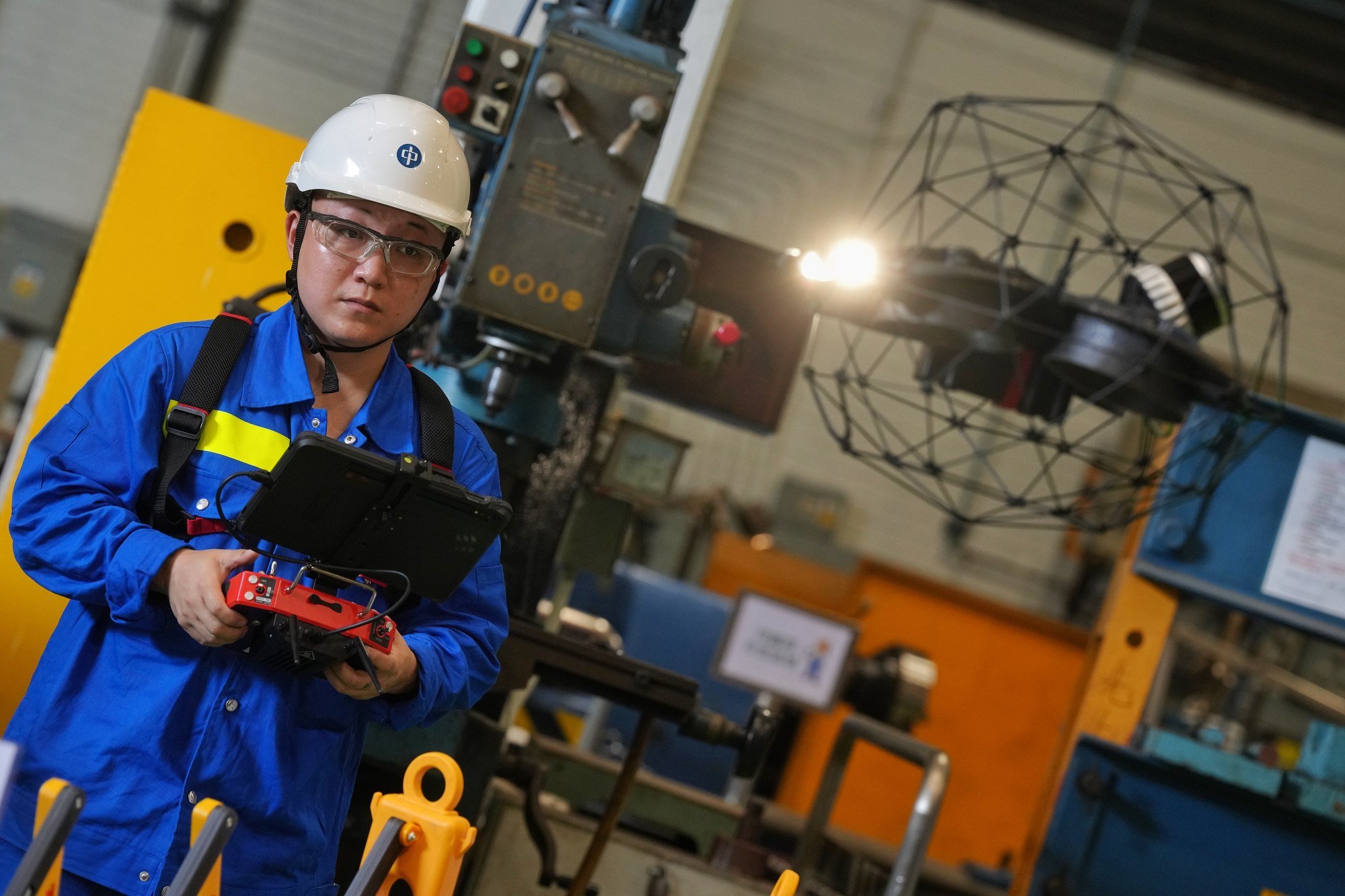
The company has two cage drones for internal checks and three outdoor drones for external checks.
“Now we can conduct inspections swiftly and we only need to apply scaffolding to specific locations where defects have been identified by drones,” Grace Wong Chung-yan, a CLP engineer, said on Tuesday. “This has made the inspection and repair work more efficient.”
Drones had helped cut the inspection time for 80-metre-tall (262-foot-tall) boilers from 12 to one or two days, while it only took two days instead of up to seven to check a 1.4km (0.87 miles) culvert using a crawler robot, which was introduced in 2021.
Wong said the drones could create three-dimensional models of the inspected facilities and comparing different versions of the mock-ups could help easily identify discrepancies.
“Facilities at power plants are huge. Finding defects is like finding a needle at sea. Some are in hidden places or dead corners, and they can easily be missed by humans,” she said. “The drones are small and flexible. They can go to places that are unreachable by humans.”
The cage and outdoor drones, as well as the crawler robot, are currently being used at two of CLP’s power plants – Castle Peak Power Station and Black Point Power Station, both in Tuen Mun, while the firm deploys only outdoor drones at Penny’s Bay Power Station on Lantau Island for external inspections.
The company used outdoor drones to examine its external facilities back in 2016, but engineers found they did not perform well in confined spaces, such as turbine halls and boilers, as the technology relied on GPS systems for location tracking, but the signals could not penetrate the thick walls.
CLP then introduced the cage drones for internal facility inspections in 2019. The technology uses the Light Detection and Ranging (LiDAR) system and sensors for positioning, which are not subject to GPS signals. Carbon fibre cages surround the drones to help avoid collisions.
“Drones can keep an eye on the facilities, but cleaning and repairs are still done by humans,” Wong said.
According to Ng Ki-on, the firm’s director of generation engineering, its use of technology had matured recently. He added that the company was trying to develop equipment to carry out simple maintenance work.
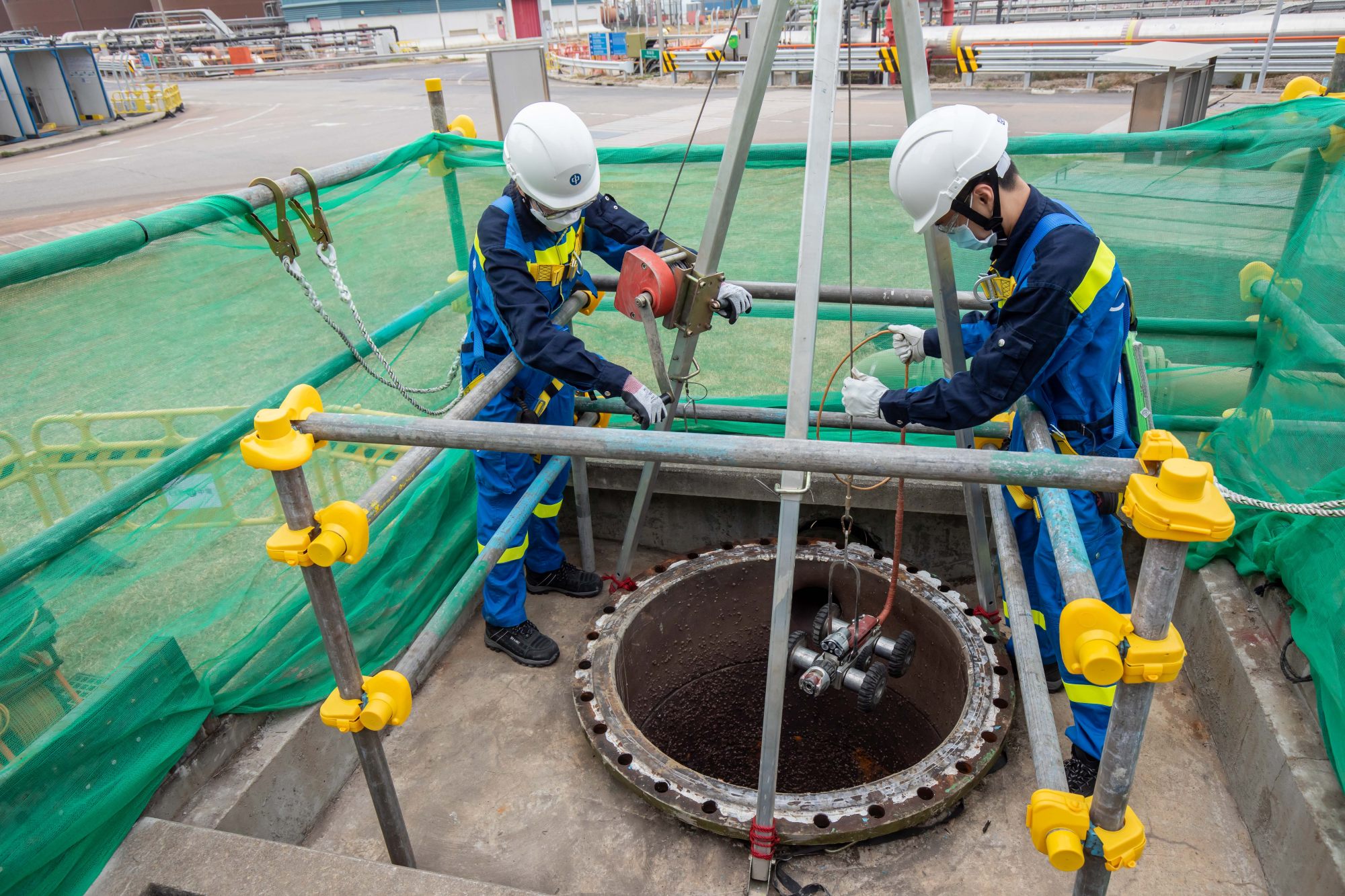
“We’ll try to develop some drones which can do maintenance work. But that will not be easy,” he said.
The drones have helped reduce inspection expenses, according to the company.
“A cage drone costs hundreds of thousands of Hong Kong dollars and can be used multiple times, but setting up full-scale scaffoldings can cost HK$2-3 million every time,” Ng said.
CLP has been using the crawler robot to check its underground culverts since 2021, which has reduced inspection times by more than half.
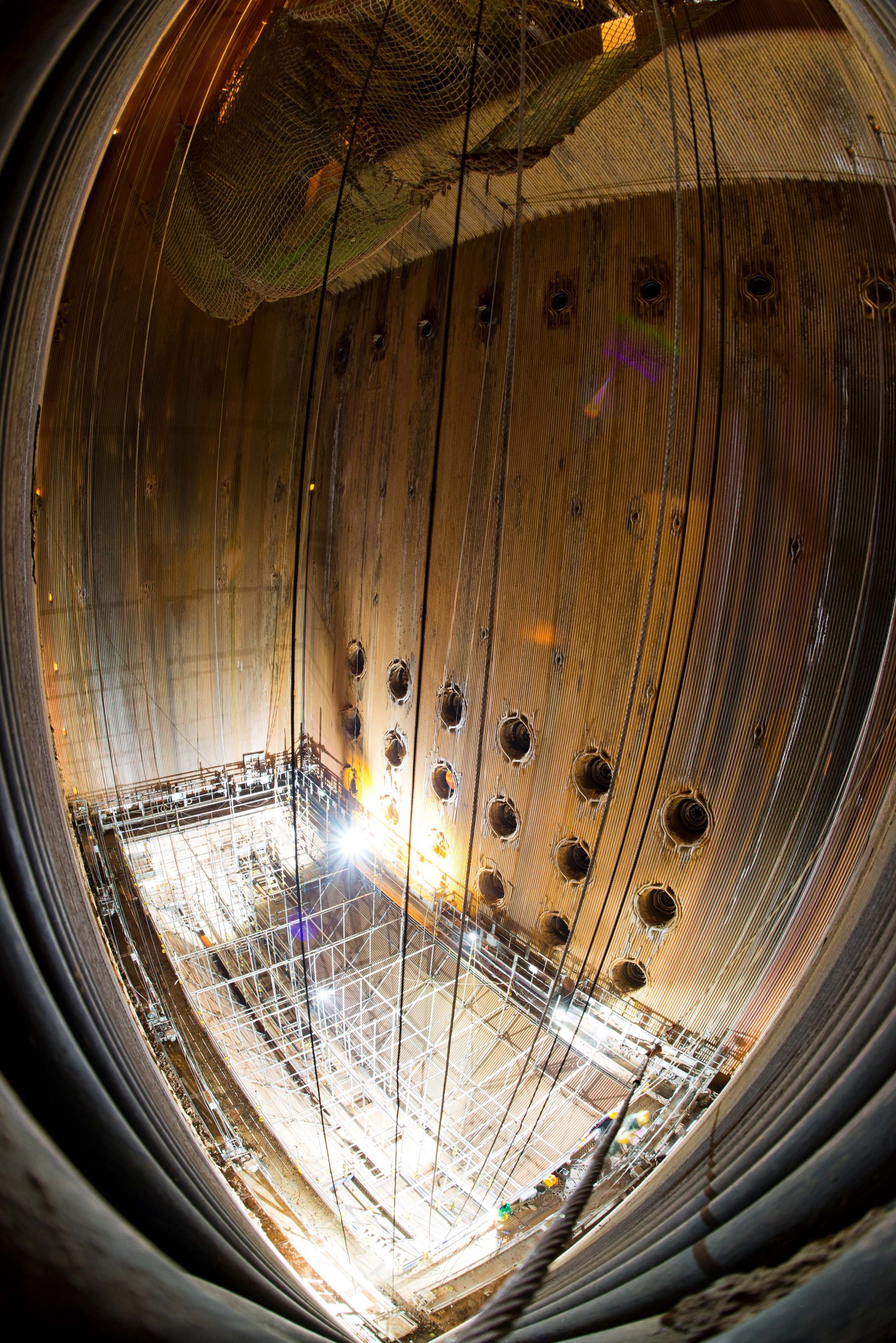
“Human inspectors had to carry equipment weighing more than 10kg [22lbs] to walk down the culverts. And some parts of the culverts are just 1.8 metres tall, and an adult man would have to bend down for such a heavy weight to pass through them, which is very demanding on the body,” said Selena Yang Huimin, a senior engineer at CLP.
“With footage filmed by the robot, we can formulate a more accurate maintenance strategy, and avoid having humans working in risky and confined spaces.” – South China Morning Post